Our industrial activity began in 1933 in the mineral foundry products sector, with the supply of coal and bentonite for the green molding process.
High-performance and innovative solutions guarantee our customers high performance of the systems and superior quality of the castings, essential in today’s competitive market.
We offer a wide range of bentonite and coal for green molding, as well as silica sands and shell molding products. Our offer is completed by the laboratory and green moulding sand analysis service, in addition to continuous customer support which guarantees the availability of essential information and the resolution of production problems.
Green Sand Casting Process
Our premixed bentonite/coal dust/additives are formulated according to the individual needs of each customer, created to achieve the best yield depending on the specific type of facility and production.
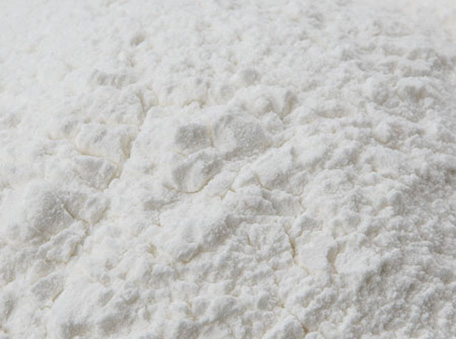
Starch
Our PRETAP – QUELL MELL – GELAMID starch product line, blended with our premixes, guarantees optimal moisture control in difficult facility settings or when the temperature is particularly high.
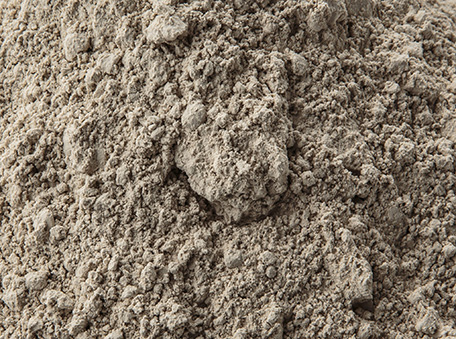
Bentonite
The BENTOCOL® range includes sodium bentonite of various origins, subdivided according to the characteristics required by the type of moulding system and the size and nature of the casting. Thanks to our wide range of options, as well as our close and transparent relationships with our customers, we are able to select the ideal bentonite for each type of production.
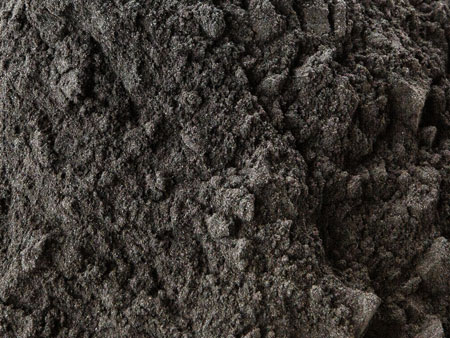
Bentonite/Coal Dust Mixtures
Our PREMIX formulas are adapted to suit different requirements, and the percentages of bentonite and coal dust are determined according to each customer’s needs. Carefully selected coal dust, with high levels of lustrous carbon, results in particularly beautiful castings free from any surface defects.
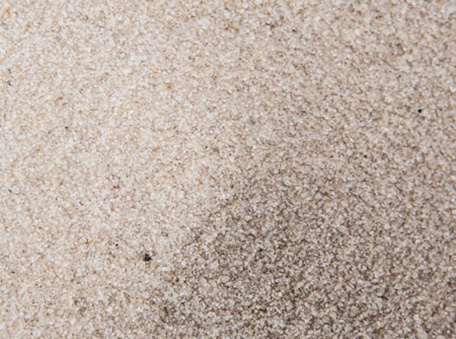
Silica Sand
Our silica sand, sourced from quarries selected for their purity, is able to provide an optimal silica skeleton, ensuring that the castings are free from defects caused by impurities or thermal expansion.
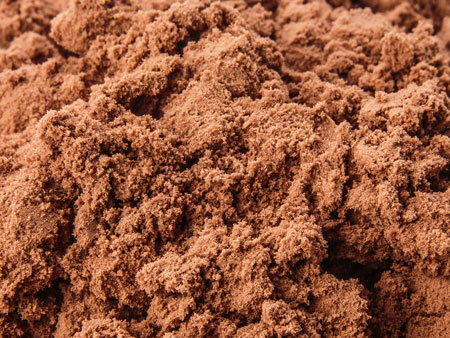
Sand for Non-Ferrous Metals
Our special ECOBOND sand is ready to use and suitable for high-precision casting of non-ferrous metals (aluminium, bronze, brass), ensuring surface finishes that are qualitatively comparable to shell moulded products.
Shell Moulding Process
The shell moulding process uses sand that is pre-coated with a thermosetting resin.
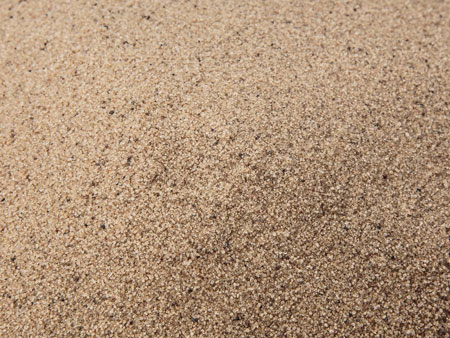
Pre-Coated Sand
The quality of the sand used, combined with a reliable and consistent process, ensures that our range of PRE-COATED SAND is compatible with all types of cores. Additionally, our specific formulas are created to handle situations where the core is particularly stressed and at risk of penetration or sintering.
Sand/Resin Casting Process
The sand/resin casting process requires high-quality, pure and consistent sand, which does not affect the action of the resin and/or catalyst. Available in a full range of grain sizes, foreign silica sand provides excellent results in terms of quality and consistency for all types of production.
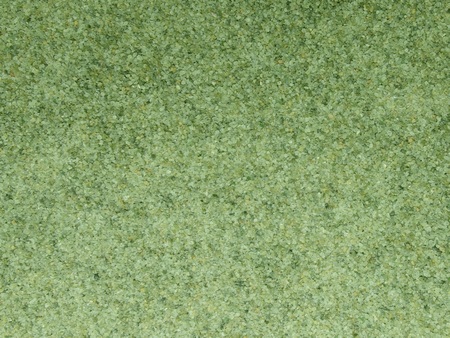
Olivine sand
Thanks to its high sintering point and low coefficient of thermal expansion, our olivine sand is particularly ideal for casting manganese steel and green sand casting iron, as these materials are especially prone to defects.
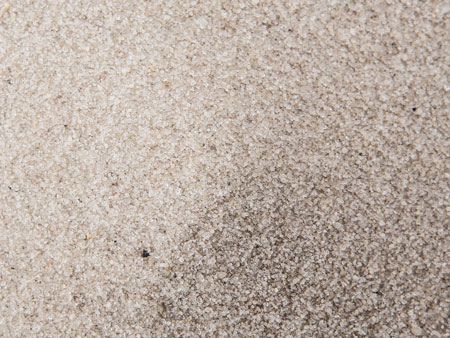
Silica Sand
Our SILICA SAND, sourced from quarries selected for their purity, is able to provide an optimal silica skeleton, ensuring that the castings are free from defects caused by impurities or thermal expansion.
Slag Removal
The slag removal process is carried out by dispersing natural granular perlite over molten cast iron. The coagulating and agglomerating effect of perlite allows slag to be easily removed from ladles and kilns.
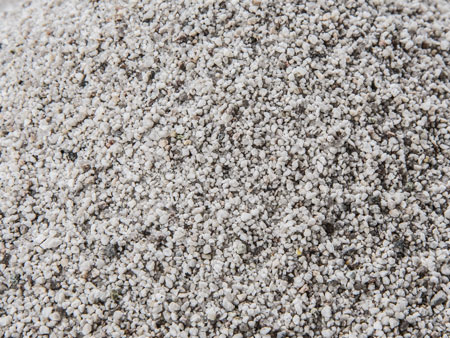
Perlite
DESCORIL, our natural perlite, is available in two different grain sizes specifically selected to remove slag from ladles or furnaces, formulated for use on both cast iron and steel.
Auxiliary Casting Products
Lubricating powders and sealing strips to optimise the yield and quality of the various steps in the green sand casting process.
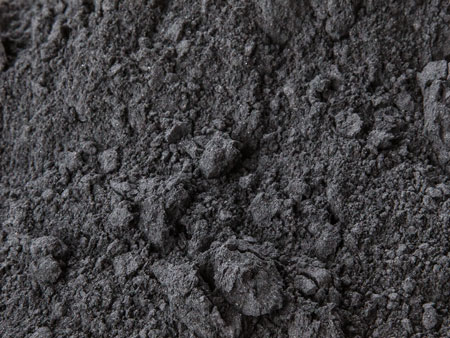
Graphite
Our GRAPHITE boasts impressive lubricating and refractory values: AMORPHOUS GRAPHITE, 65/70 C, is formulated to be dispersed in water with an appropriate binder in order to coat sand resin moulds, improving the refractory qualities of the mould and the surface finish of large castings; SILVER GRAPHITE 90 C is intended to be dusted on green sand moulds where the surface finish of the castings needs to be perfect.
Services and Technical Support
In foundry processes, technical support and close cooperation between supplier and customer are essential for maintaining the high quality standards of the Italian foundry sector in this difficult and competitive environment.
Services and Technical Support
The service department is made up of specialised technicians who carry out periodic visits and timely interventions, monitoring and preventing any casting issues and surface defects.
Laviosa-FoundryLab Service
Our foundry sand consulting and analysis service offers a range of control activities based on periodic analysis and active monitoring of sand performance according to different production types.
Laviosa is a member of:
Amafond and the Institute of Indian Foundrymen
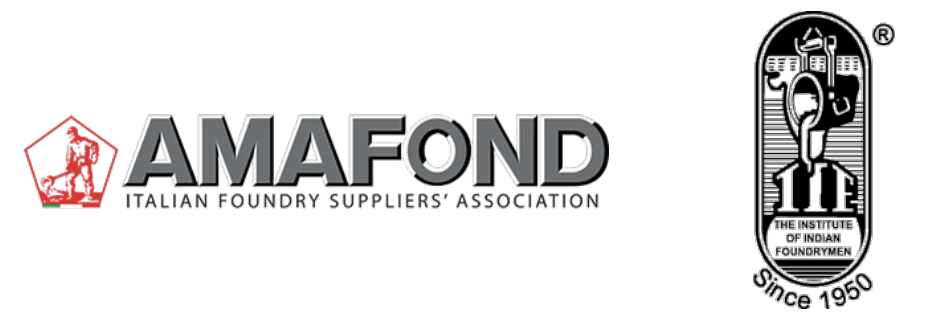